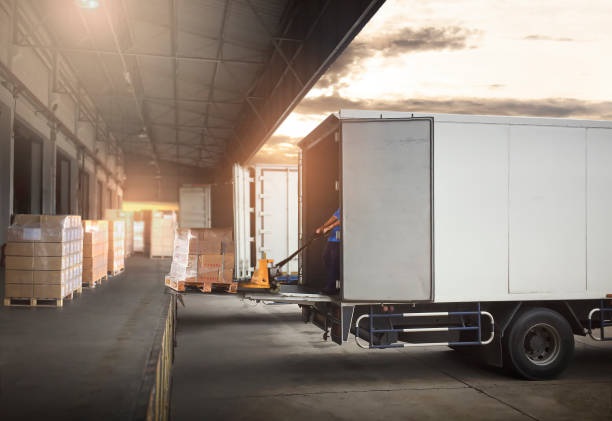
When you need to see a doctor, what’s the best way to ensure a smooth and predictable experience? If you simply walk in, you might be seen right away. But the waiting room could be full of patients who arrived before you, and there’s no way to know how long you’ll have to wait. This uncertainty can disrupt your entire day.
On the other hand, scheduling an appointment enables you to plan your visit effectively. You’ll know exactly when to leave home, the time of your appointment, and roughly how long it will take. You can make plans before and after your appointment, ensuring that your day remains productive and free from unpredictable waiting times.
Similarly, dock scheduling works by assigning specific time slots for trucks to load and unload goods at a facility’s loading dock. Instead of shipments arriving at random times and causing uncertainty about product availability, scheduling enables logistics operators to forecast specific availability and delivery times with such precision that it becomes possible to coordinate direct transfers of products between trucks.
This approach speeds up the supply chain, helps avoid delays, reduces operational expenses, and fosters positive relationships with carriers and customers. Further, by implementing a scheduling system, companies can reduce costs for overhead expenses such as paying drivers overtime for waiting in traffic, making it a valuable and effective tool.
Dock scheduling offers the following benefits:
- Enhancing communication: Dock scheduling systems often integrate with other logistics management tools, allowing real-time communication between warehouse staff, drivers, and carriers.
- Reducing waiting times: By allotting specific time slots, trucks can arrive, load, and depart without unnecessary delays, reducing downtime for drivers and minimizing congestion at the dock.
- Optimizing resource utilization: Scheduled dock times enable better labor and equipment planning, ensuring that the necessary resources are available when needed.
- Improving warehouse throughput: A well-scheduled dock increases the number of shipments that can be processed daily, leading to improved overall efficiency.
How dock scheduling works
The dock scheduling process begins when a carrier or supplier requests a time slot to deliver or pick up goods. These requests are managed through a dock scheduling system, which may be part of a larger warehouse management system or software solution. The process involves the following steps:
- Time slot request: Carriers or suppliers request a time slot for their trucks to arrive at the dock. This request may include details about the shipment, such as the type of goods, volume, and any special handling requirements.
- Time slot allocation: The warehouse manager or an automated system reviews the request and allocates a time slot based on current dock availability, the type of goods being handled, and the facility’s operational capacity.
- Confirmation and communication: Once a time slot is allocated, the system sends a confirmation to the carrier or supplier. This confirmation typically includes instructions for the driver, such as which dock to use and any specific entry or safety protocols.
- Arrival and check-in: Upon arrival, the driver checks in with the warehouse through a digital system or in person. This step confirms the truck’s presence and ensures the dock is ready for loading or unloading.
- Loading and unloading: The actual loading or unloading of goods occurs during the assigned time slot. This step requires coordination between warehouse staff and the driver to ensure the process is completed within the scheduled time.
- Departure and documentation: After the goods are loaded or unloaded, the truck departs, and the necessary documentation is completed. This might include bills of lading, delivery receipts, and any other paperwork required to finalize the transaction.
Challenges in dock scheduling
Despite its importance, dock scheduling can be challenging, particularly for large facilities or those dealing with a high volume of shipments. Some common challenges include:
- Last-minute changes: Unforeseen delays, such as traffic or weather, can disrupt schedules, requiring last-minute adjustments that can cause a ripple effect on other shipments.
- Resource constraints: Limited dock space, labor shortages, or insufficient equipment can lead to scheduling conflicts and delays.
- Complexity in coordination: Coordinating between multiple carriers, suppliers, and warehouse operations can be complex, especially if there is a lack of communication or incompatible scheduling systems.
- Capacity management: Overbooking or underutilizing dock space can result in inefficiencies, either through congestion or wasted resources.
Modern solutions to dock scheduling challenges
Many logistics companies are turning to advanced dock scheduling software that leverages data analytics, real-time tracking, and automation to address these challenges. Our self-designed dock scheduling system, built in collaboration with our clients, enhances your loading and unloading facility experience. This digital, web-based solution reduces downtimes, improves the planning of internal resources, and provides early information about the availability of procured materials.
- Automated scheduling: Our platform can allocate time slots based on real-time data, considering factors such as current dock occupancy, expected traffic, and shipment priorities.
- Real-time updates: Integrated communication tools enable our scheduling system to provide real-time updates to all stakeholders, allowing for quick adjustments if a delay or other issue arises.
- Data-driven insights: By analyzing historical data, our software can optimize scheduling patterns, predict peak times, and identify areas for improvement.
- Scalability: We’ve incorporated scalability into our scheduling solution, adaptable to meet the needs of any facility, from small warehouses to large distribution centers with multiple docks.
Looking ahead
Dock scheduling is not just about timing but also optimizing the flow of goods from supplier to end customer. Its future relies on integrations with other supply chain components, such as transportation management systems and inventory management systems. Further, incorporating control towers into dock scheduling systems permits greater precision and adaptability to changing conditions.
Learn more
Explore our Services and Solutions portfolio to learn how we can deliver a total solution that helps you save costs, minimize turn times, and gain a competitive edge in the global logistics market. If you’re interested in partnering with us, visit our Contact page to get in touch.