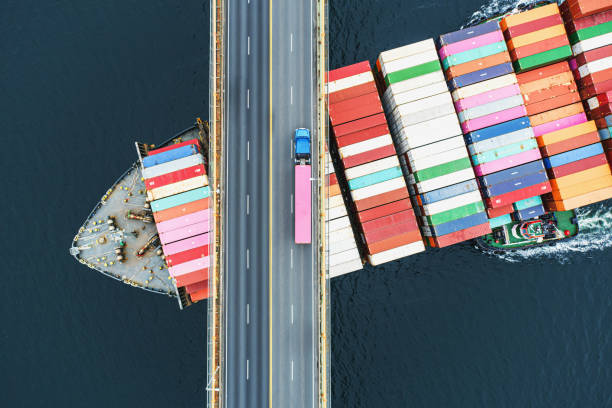
Logistics involves moving, storing, and distributing goods and services to meet customer needs. It includes managing customer orders across different business functions.
In a company’s production or operations department, ensuring timely materials delivery to the factory and finished product delivery to the customer is crucial. Doing so involves coordinating production runs, controlling inventory, and minimizing transportation costs.
The purchasing function determines the quantity and timing of deliveries through material contracts. The procurement team, reporting to the factory manager, selects suppliers that impact transportation decisions. Clear communication with the purchasing department, whether suppliers are local or global, is essential for on-time deliveries.
The finance department closely monitors logistics operations. Effective management of vehicles, warehouses, and distribution centers significantly impacts return on investment and net assets, reducing inventory and distribution costs for the entire organization.
Good delivery processes adhere to four important concepts:
- Price: Offering price discounts to encourage larger purchases, and logistics professionals can align quantity discounts with full truckloads to reduce delivery costs
- Product: A product’s physical attributes, like size, weight, shape, and packaging; these attributes influence the most cost-effective way to load a truck and determine storage in warehouses and distribution centers
- Promotion: Requires well-planned sales and promotions that coordinate with logistics to ensure sufficient product availability; if a sales campaign exceeds expectations, the logistics team must respond with rapid delivery procedures
- Place: Marketing decisions that influence how products are sold, whether through wholesalers, retailers, or directly to customers online; these decisions must align with distribution network capabilities, including warehouse locations and transportation routes
An effective system for fulfilling customer orders is essential for success in sales and promotions. A great delivery process can lead to repeat customers, while a poor one can result in permanent customer loss.
Logistics workflow
Logistics directly affects customer service levels and revenues, making it essential for company success. Coordinating logistics efforts with operations, purchasing, and finance is crucial. Understanding logistics is key to meeting customer demands promptly and efficiently.
The key components of a logistics workflow are:
- Movement: Logistics involves transporting goods from suppliers to factories and from factories to customers. Logisticians plan and manage these movements throughout the supply chain.
- Storage: Materials or products may be temporarily stored in warehouses. This activity happens when you take advantage of price discounts by making large purchases or storing finished products until customers order them. It is common for seasonal items to be produced year-round but sold during specific seasons.
- Distribution: Products are shipped to distribution centers or distributors like Amazon or Alibaba before reaching retail stores or end customers.
- Return: Logistics also manages the return of products that do not work properly or need to correct delivery mistakes. This involves moving goods and materials back through the supply chain.
The Council of Supply Chain Management Professionals defines logistics management as “…[the] part of supply chain management that plans, implements, and controls the efficient, effective forward and reverse flow and storage of goods, services, and related information between the point of origin and the point of consumption to meet customers’ requirements.” To succeed, it requires four key capabilities:
- Understanding demand: You must be aware of the demand for their products, which often necessitates a team of analysts and close communication with marketing, purchasing, and operations.
- Business strategy: Planning an effective strategy involves determining warehouse locations, scheduling deliveries, and optimizing order fulfillment.
- Inventory and transportation management: Logisticians oversee inventory from raw materials to finished goods and manage transportation via truck, rail, ship, and airplane.
- Support services: Efficient customer communication and return management are essential.
These overarching concepts apply whether you’re planning your inbound, outbound, or reverse logistics strategy.
Inbound logistics
Inbound logistics involves getting the necessary parts, components, and materials to the factory or assembly plant at the right time to produce the final product. For example, aircraft manufacturers assemble airplanes from millions of parts supplied by various companies. This complex process requires efficient management to ensure timely deliveries and avoid delays in the final product.
Important considerations for effectively managing inbound logistics include:
- Supplier selection: Choosing reliable suppliers who deliver defect-free materials is crucial. Proximity to the factory can reduce the risk of delivery interruptions.
- Distribution center management: You may buy large volumes to secure price discounts, requiring storage and timely distribution to the factory. Doing so often involves using independent distributors, but close management is necessary to prevent supply shortages.
- Transportation coordination: Working closely with suppliers to ensure timely deliveries is essential, whether materials are picked up or delivered. It’s also important to understand the delivery capacity of all involved parties, both in terms of the ability to ship and the ability to receive.
Outbound logistics
Outbound logistics focuses on keeping customers happy by ensuring timely product delivery. It refers to the efficient movement of products from factories to distribution centers and through stores to the end customer. The goal is to have the right products in the right places, necessitating continuous improvement of distribution processes to reduce delivery costs and enhance efficiency.
For example, a major retailer owns numerous stores that carry a vast array of products from assorted suppliers across the globe. The retailer’s distribution centers receive large volumes of merchandise, which are then broken down into smaller portions for individual stores. The size, number, and location of distribution centers in the retailer’s chain are vital to preventing out-of-stock situations.
To support its outbound logistics, the retailer also owns and operates one of the largest truck fleets in the U.S. Instead of expanding its fleet, it contracts with independent truck operators to handle extra deliveries during busy periods.
The infrastructure needed to support outbound logistics can vary from company to company and from industry to industry. You should evaluate your product journey from start to finish to understand where optimizations are necessary and implement management mechanisms accordingly.
Reverse logistics
Reverse logistics occur when goods move in the opposite direction through the supply chain. A reverse flow of goods can occur for various reasons, such as defective products, trade-ins, or warranty repairs. If unmanaged, a high volume of returns or exchanges can hinder the timely delivery of products to customers, making reverse logistics crucial for many businesses. For more information, refer to our Reverse Logistics article.
Learn more
Check out our Services and Solutions portfolio to discover the many ways we can assist you in navigating these critical aspects of your supply chain. If you’re interested in partnering with us, visit our Contact page to get in touch.