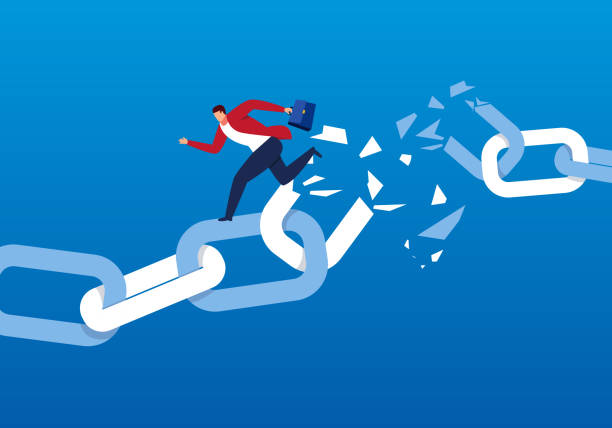
Supply chain disruption.
These three words can scare even the most experienced logistics manager.
While we frequently discuss the importance of avoiding supply chain disruptions, what does the term actually mean? Does your company fully understand the implications of such disruptions, and do you have a robust redundancy plan in place to address them?
In a “disruption” scenario, a supply chain is affected by various specific, interlinked issues that interrupt operations.
These disruptions are not merely abstract “delays;” they create a chain of logistical breakdowns that compound costs, inflate prices, and reduce the reliability of goods reaching their destinations on schedule.
Real-world examples of logistical disruptions include the following:
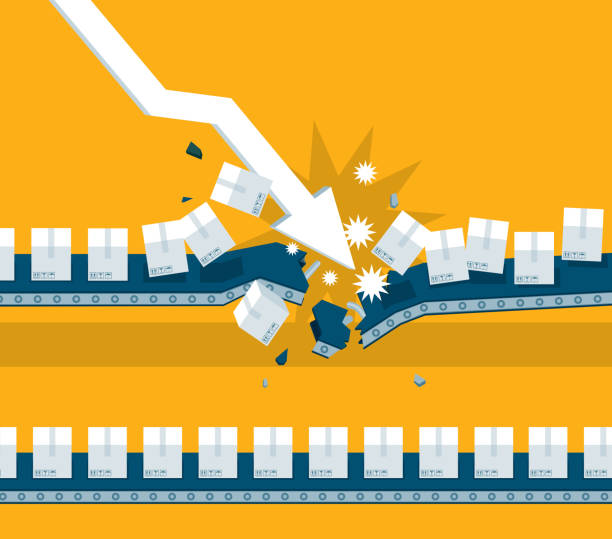
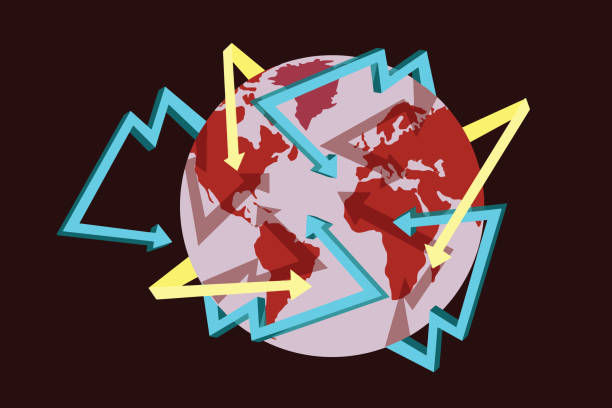
Delayed transportation: Geopolitical situations like the Russia-Ukraine conflict can interfere with essential transportation routes. For instance, restrictions on airspace compel flights to take longer detours, leading to higher fuel expenses and extended travel durations.
Likewise, rail connections, especially those between China and Europe, may face disruptions or rerouting, which can drastically reduce the speed of goods movement.
Port congestion and container shortages: When demand surges sharply, ports may struggle with congestion, as has occurred in recent years at various United States and European ports.
Ships often encounter significant delays due to a buildup of loading and unloading tasks. Container shortages can worsen the issues, causing goods to be stuck without quick shipping solutions.
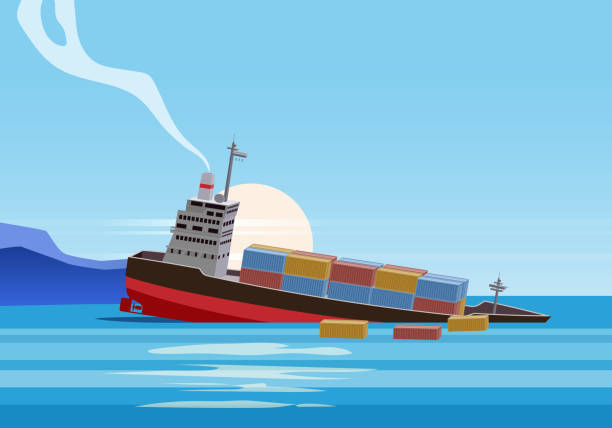
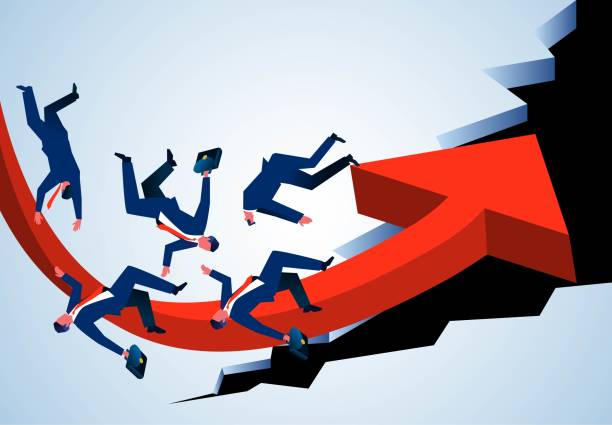
Labor shortages: A shortage of skilled labor greatly affects warehousing and transportation. For example, fewer truck drivers can cause delays in dispatching goods, disrupting delivery schedules.
Additionally, when warehouses are understaffed, sorting and processing take longer, leading to increased wait times in the supply chain.
Material scarcity and inflation: Supply chain disruptions cause shortages of essential materials, leading to increased costs. Metals like nickel and aluminum, often sourced from conflict areas or specific locations, become more challenging to obtain.
Such scarcities raise prices and place inflationary pressures on various products, including electronics and packaging.
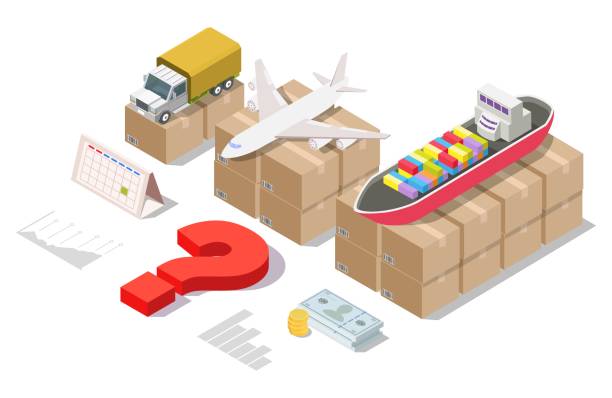
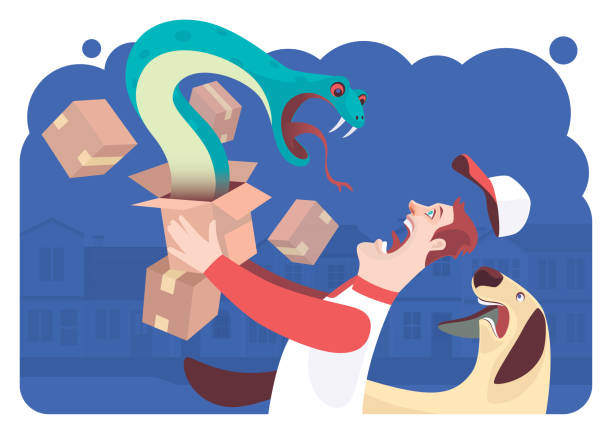
Last-mile delivery failures: Last-mile logistics refers to the delivery of goods from distribution centers to their final destinations.
Problems such as incorrect address data and increased rerouting costs can arise.
Companies that use fixed routes or manual processes often have trouble adapting quickly. As a result, they face missed deliveries and unhappy customers.
In the event of a disruption, self-managed logistics operations often lack the tools or capital to reroute or find alternative suppliers quickly. In contrast, a 4PL can swiftly adapt to unexpected situations through its industry experience, access to dedicated resources, established networks, and predictive models. Centralized control towers leverage advanced technologies that monitor transport routes, material sourcing, and workforce availability to provide total supply chain health and visibility across all logistics areas.
Learn more
Explore our Services and Solutions portfolio to discover the various options we offer for proactively managing disruptions caused by geopolitical issues or labor shortages while maintaining supply flow and controlling costs. If you’re interested in partnering with us, visit our Contact page to get in touch.